Optimized Use of Consumption and Staging with PP-EWM (Extended Warehouse Management) Advanced Production Integration
Hello, in this article we will talk about PP-EWM integration and we will tell you how production integration works in the most basic and most optimized way.
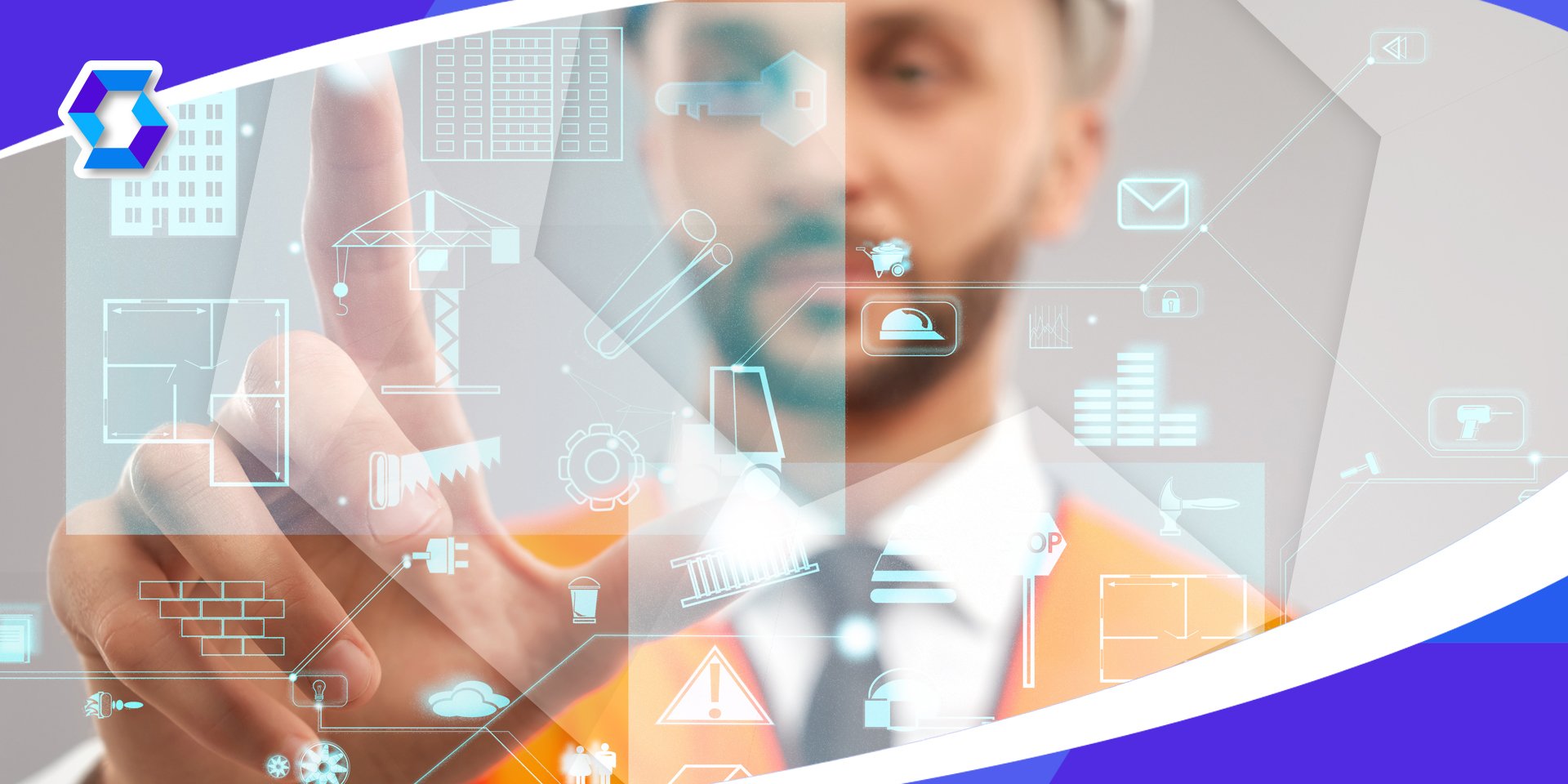
In order to make the Production and Storage processes more effective and useful, we will perform the consumption and ready-made parts of the processes through web applications rather than the standard GUI screen. With this, we will be able to advance production and consumption faster and easier, and we will be able to correct any confusion that may occur in a simple way.
In our example scenario, we have a production warehouse location and an EWM warehouse feeding this production warehouse location. In addition, production is carried out with one production supply area belonging to the production warehouse area.
The processes proceed as follows;
- The production order is opened and the production process begins.
- The production script is run.
- Ready stock warehouse tasks are approved.
- Consumption transactions are performed and related records are updated.
- Depending on the production order, transport units are created for the goods receipt.
- Goods receipt is performed and then storage is done.
All these processes can be carried out directly on the standard without the need for any development.
Production processes can be implemented completely as standard and there is no need for any development. With the right adaptation and master data, you can manage all of your production processes with ewm.
PP-EWM (Production Planning and Extended Warehouse Management) integration refers to an integration process between production planning and extended warehouse management. The advantages and disadvantages of this integration can be:
Advantages:
Integration improves data and information flow between the production planning process and warehouse management. This enables better coordination, collaboration and efficiency.
Better synchronization between production planning and inventory management is achieved. This allows for more precise control of inventory levels and optimization of stock.
Thanks to real-time data sharing, important information such as inventory status, production progress and logistics activities can be tracked instantly.
PP-EWM integration helps manage inventory and storage usage more effectively. This can reduce operating costs.
Disadvantages:
The integration process can be complex and some technical difficulties may be encountered at the beginning. Therefore, it is important that the integration is configured and managed correctly.
Cross-system compatibility issues may arise. There may be different data formats and protocols between the production planning system and the extended warehouse management system, which can complicate the integration process.
The software and hardware investments required for integration can be costly. This can sometimes be restrictive for small businesses.
Data integrity and security issues should be considered. Along with the integration process, data transfer and sharing must be carried out securely and protected against unauthorized access.
These advantages and disadvantages are presented to provide an overview. Every business situation may be different, so the specific advantages and disadvantages of PP-EWM integration may vary depending on the business needs and circumstances.
First, we create and execute our production order.
The document is saved by clicking the Save button.
After the production order is created, the production order is ready operations are executed. While the ready-made process normally proceeds on the screen with the /SCWM/STAGE tcode, we will advance this process through the Web Dynpro App. We will talk about the advantages of this in a moment.
We recommend you to take a look at our blog titled “Adding Screens to SAP GUI for Web Dynpro Application” regarding the installation of the readymade application for production.
Application name: /SCWM/MFG_STAGING
The production order number is given to the search criteria and the FIND button is pressed.
Warehouse tasks can be created by selecting the relevant lines and entering the recommended quantities after the ready-made staging are received.
Apart from creating a warehouse task, many different operations can be performed from the related links button.
The benefits of using web applications are, for example, if the wrong amount is consumed, reverse registration can be easily obtained through the WDA application, the production supply area can be emptied, changes can be made on the ready-made household consumption amounts, and similar processes can be managed. All these processes can be done on a single screen.
After wt are created, they can be viewed on the /SCWM/MON screen.
The warehouse order for warehouse tasks is as follows.
Relevant warehouse tasks will be confirmed with the terminal. (You can confirm in many different ways. I wanted to use terminal in this example.)
Warehouse order number is given and ENTER button is pressed.
Adres, TB, Ürün gibi alanlar terminal ile okutularak ilerlenir.
After the warehouse task is approved, it is necessary to carry out the consumption process next. The following application must be opened to make the consumption process.
Application name: /SCWM/MFG_CONSUMPTION
Üretim sipariş numarası ilgili alana yazılarak tüketim butonuna basılır. (tüketime ait ters kayıtlar ters kayıt butonuna basılarak yapılabilmektedir.)
After the consumptions are made, it is now possible to enter goods from production.
The production order number is entered and the ENTER button is pressed.
The TB must be created to run the respective process. We can create TB with the help of the button marked in red below.
Warehouse tasks are confirmed as shown below.
After the consumption and ready-made transactions are done, we will carry out the goods receipt transactions to the EWM warehouse. The delivery document can be accessed by giving the production order number to the field below.
Goods receipt is complete.
Some benefits of using the Web Dynpro application in PP-EWM integration can be:
User-Friendly Interface: Web Dynpro offers a user-friendly interface. Users can easily perform operations related to PP-EWM integration, view and manage data. This improves the user experience and allows users to take action quickly and effectively.
Real-Time Data Access: Web Dynpro provides real-time data access. This allows users to get instant inventory status, production progress, order status, etc. provides instant access to information such as Based on up-to-date data, users can make better decisions and optimize their operational processes.
Customization and Flexibility: Web Dynpro allows businesses to customize their PP-EWM integration according to their needs and preferences. Businesses can customize the user interface and its functions, adapting it to suit their business processes and user needs. This provides flexibility and adaptability.
Productivity Improvement: Web Dynpro helps users perform operations faster and more efficiently. Easy to use, optimized user interface and user-oriented design allow users to save time and make business processes more efficient.
Ease of Integration: Web Dynpro makes PP-EWM integration easy. It can be seamlessly integrated into existing systems and data flow can be provided. This makes the PP-EWM integration process faster and smoother.
These benefits are the general advantages that the Web Dynpro application can provide in PP-EWM integration. However, different benefits may arise in certain situations, as the needs and requirements of each business may be different.